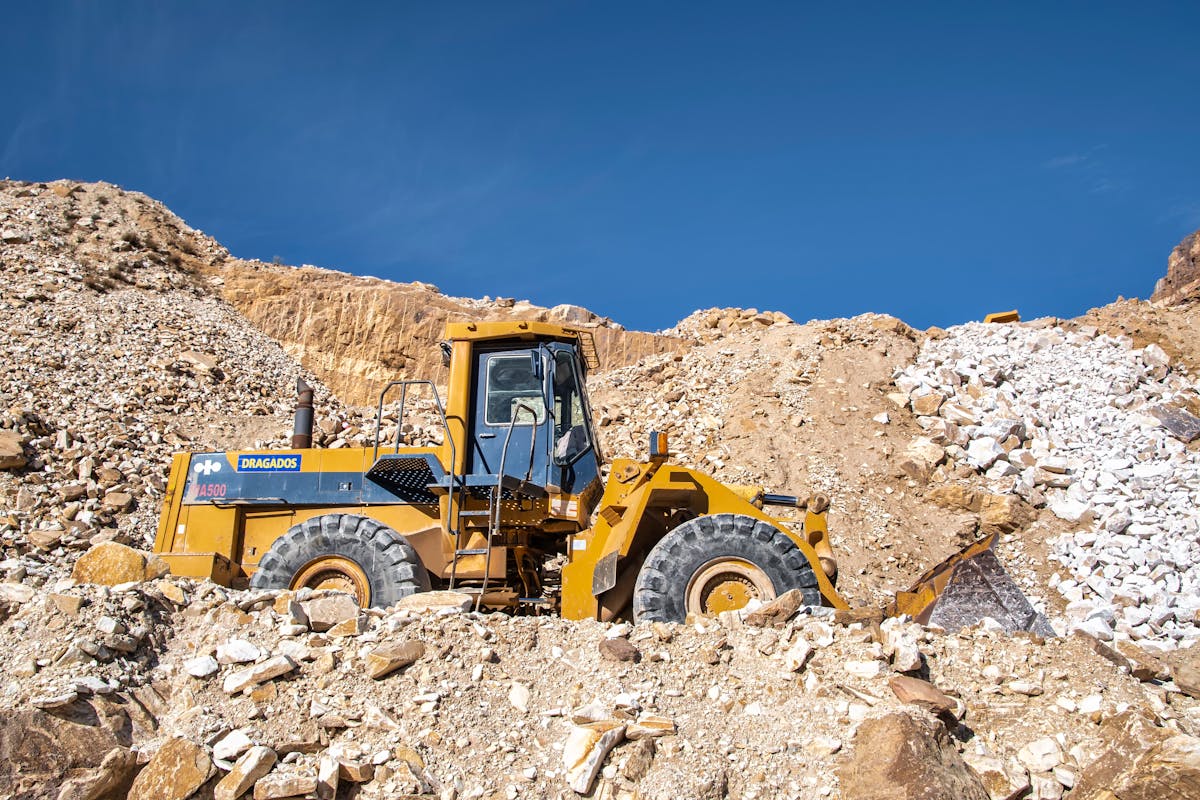
Introduction
Mining has been a cornerstone of Southern Africa’s economy for centuries, with rich deposits of gold, platinum, diamonds, and other minerals driving economic growth. As mining practices evolved, so did the machinery used to extract these valuable resources. Over time, the introduction of modern heavy-duty equipment and skilled mechanics has significantly improved efficiency, safety, and reliability in the industry.

In the early days of mining, manual labor and rudimentary tools such as picks, shovels, and hammers were the primary means of extraction. Indigenous communities and early European settlers used simple excavation methods, often relying on human and animal power to transport materials.
By the late 19th century, with the discovery of gold in the Witwatersrand Basin and diamonds in Kimberley, mining operations expanded rapidly. Steam-powered equipment such as hoists, drills, and pumps were introduced to increase productivity. Rail tracks and mule-drawn carts were commonly used for material transport within mines.
Southern Africa is endowed with vast mineral wealth, positioning mining as a linchpin of economic development. However, the industry is beleaguered by systemic inefficiencies, technological obsolescence, exorbitant operational expenditures, and entrenched corruption. The strategic integration of Western heavy mechanics efficiencies—pioneered by industry leaders such as Caterpillar (CAT), Komatsu, (watch the Changing the Entire Landscape With Big Komatsu Machines Powerful Heavy Equipment in Action) and Hitachi Construction Machinery—can revolutionize the region’s mining landscape by enhancing productivity, curtailing downtime, and bolstering safety metrics.

Understanding Western Heavy Mechanics Efficiencies

Western heavy machinery manufacturers have consistently spearheaded innovations in mining technology, focusing on automation, predictive maintenance, and optimized machinery design. Core advancements include:
- Advanced Automation and Robotics: Autonomous drilling rigs, AI-driven haul trucks, and robotic conveyor systems exponentially enhance extraction rates while mitigating human error and workplace hazards.
- Predictive Maintenance and IoT Integration: Sophisticated diagnostic tools, real-time telemetry, and sensor-driven prognostics preempt equipment malfunctions, significantly reducing unscheduled downtimes.
- Energy Optimization and Emission Reduction: High-efficiency engines, hybrid-electric loaders, and low-emission haul trucks—such as those developed by CAT and Komatsu—reduce fuel consumption, operational overheads, and environmental footprints.
- Ergonomic and High-Precision Equipment: Machinery featuring advanced human-machine interfaces (HMIs) ensures operator comfort, improves precision in mineral extraction, and enhances workforce efficiency.
- Data-Driven Operational Intelligence: Cutting-edge analytics platforms, such as those integrated into Hitachi’s autonomous mining solutions, facilitate optimal decision-making in resource allocation and supply chain logistics.
Comparative Analysis: Current Mining Output vs. Western Mechanization
Current Mining Landscape in Southern Africa
Mining operations in Southern Africa exhibit stark disparities between industrialized mining firms and informal, small-scale, or illegal operations. A significant portion of gold production comes from artisanal and small-scale mining (ASM), which, although labor-intensive, operates with rudimentary tools and outdated techniques. Illegal gold panning operations contribute to substantial mineral output, but at the cost of inefficiencies, environmental degradation, and revenue loss to national economies.
Challenges in the current mining framework include:

Pic from NPR – Tommy Trenchard for NPR
- High Resource Waste: Inefficient extraction methods lead to significant mineral loss, with ASM operations recovering only a fraction of the potential yield compared to mechanized systems.
- Environmental and Safety Hazards: Unregulated mining causes land degradation, water pollution, and hazardous working conditions, often leading to fatalities.
- Revenue Leakages: A substantial portion of minerals, particularly gold, is smuggled or sold on the black market, depriving governments of crucial tax revenue.
- Low Processing Capacity: The lack of modern refineries forces Southern African nations to export raw minerals rather than processed commodities, limiting value addition.
Projected Output with Western Mechanization
If Southern Africa fully adopted Western mining methodologies, including CAT, Komatsu, and Hitachi machinery, the economic and operational output would transform dramatically:
- Enhanced Extraction Efficiency: Automated equipment can process significantly higher tonnage per day, reducing reliance on manual labor and minimizing extraction losses.
- Higher Yield per Mine Site: Mechanized operations typically achieve over 90% material recovery efficiency, compared to ASM operations, which often operate at below 50% efficiency.
- Formalization of Informal Mining Sectors: With access to high-capacity machinery, small-scale miners could integrate into formal supply chains, ensuring regulated output and higher economic returns.
- Revenue Growth and Industrial Expansion: Implementing advanced machinery would support localized mineral refining, creating jobs and reducing the need to export raw minerals. According to a correspondent from Sennor Group Inc, a Canada-based leader in ultra-class heavy mining equipment maintenance and consulting, “Southern Africa possesses immense untapped potential that necessitates full-scale access to heavy equipment tradespeople. Furthermore, the integration of modern mechanization will empower African states to transition from raw material exporters to producers of refined mineral commodities, fostering localized industrialization and economic self-sufficiency.”
- Job Creation through Technological Upskilling: Although mechanization reduces manual labor requirements, it creates new roles in machinery operation, maintenance, and mining analytics, leading to a more technically skilled workforce.
Economic and Operational Benefits of Western Mechanization
1. Maximized Productivity and Yield Efficiency
The incorporation of automated and precision-controlled mining equipment streamlines production cycles, augments ore recovery rates, and sustains high-quality yield standards. Mechanized solutions allow for round-the-clock operations, enhancing annual throughput volumes.
2. Reduced Maintenance Expenditures and Downtime Risks
Western manufacturers such as CAT and Hitachi deploy AI-enhanced diagnostic systems to facilitate preemptive maintenance protocols, shifting mining enterprises from reactive breakdown responses to proactive asset management. This transition curtails unexpected shutdowns and mitigates maintenance-related capital expenditures.
3. Augmented Workforce Safety and Hazard Reduction
Remote-operated machinery, autonomous haulage systems, and advanced collision-avoidance technologies significantly reduce direct human exposure to high-risk environments, thereby lowering injury rates and enhancing workplace safety compliance.
4. Cost Efficiency and Sustainable Resource Utilization
Energy-efficient engines and Komatsu’s hybrid powertrain technology optimize fuel consumption, driving down operational costs while aligning mining activities with global sustainability mandates.
5. Strengthened Environmental and Regulatory Compliance
The adoption of Western eco-conscious mining solutions, such as Hitachi’s low-carbon haulage fleets, enables compliance with stringent international environmental regulations, fostering corporate social responsibility and reducing ecological degradation.
Hindrances to Implementation in Southern Africa
Despite the evident benefits, the regional adoption of Western heavy mechanics is encumbered by various challenges:
- Prohibitive Capital Expenditure: The acquisition and integration of state-of-the-art mining equipment demand significant upfront investments.
- Deficit of Technically Skilled Labor: A shortage of specialized training programs hampers workforce readiness for high-tech machinery operation.
- Infrastructure Deficiencies: Inconsistent power supply and inadequate logistics networks obstruct seamless mechanization implementation.
- Institutional Resistance to Change: Legacy mining firms often exhibit reluctance toward abandoning traditional extraction methodologies.
- Corruption and Governance Failures: Corruption remains a critical bottleneck, with funds misallocation, preferential contract awarding, and lack of fiscal transparency stymying the deployment of advanced technologies.
Conclusion
The strategic adoption of Western heavy mechanics efficiencies, championed by industry titans such as CAT, Komatsu, and Hitachi, heralds a paradigm shift for Southern African mining enterprises. By embracing automation, predictive analytics, and energy-efficient machinery, regional operations can achieve heightened productivity, economic sustainability, and workforce safety. However, overcoming corruption, capital constraints, and infrastructural limitations will necessitate coordinated governmental and private sector interventions. If successfully implemented, these advancements will position Southern Africa as a formidable player in the global mining value chain, driving industrialization and fostering long-term economic prosperity.
Sources
Caterpillar Inc. – https://www.cat.com, Komatsu Mining Corp. – https://www.komatsu.com
Hitachi Construction Machinery – https://www.hitachicm.com, Sandvik Mining and Rock Solutions – https://www.rocktechnology.sandvik, Modular Mining (Autonomous Mining Tech) – https://www.modularmining.com, Wenco International Mining Systems, https://en.wikipedia.org/wiki/Modular_Mining_Systems
Other African mining news
BHP enters into ‘earn-in’ agreement to fund Botswana copper projects
Australia’s biggest miner boasts operations in Australia, Chile and Canada, and now it’s making a new play for Africa. Read more:
Discover more from SBNN
Subscribe to get the latest posts sent to your email.